How Top Fleets Manage High-Risk Drivers
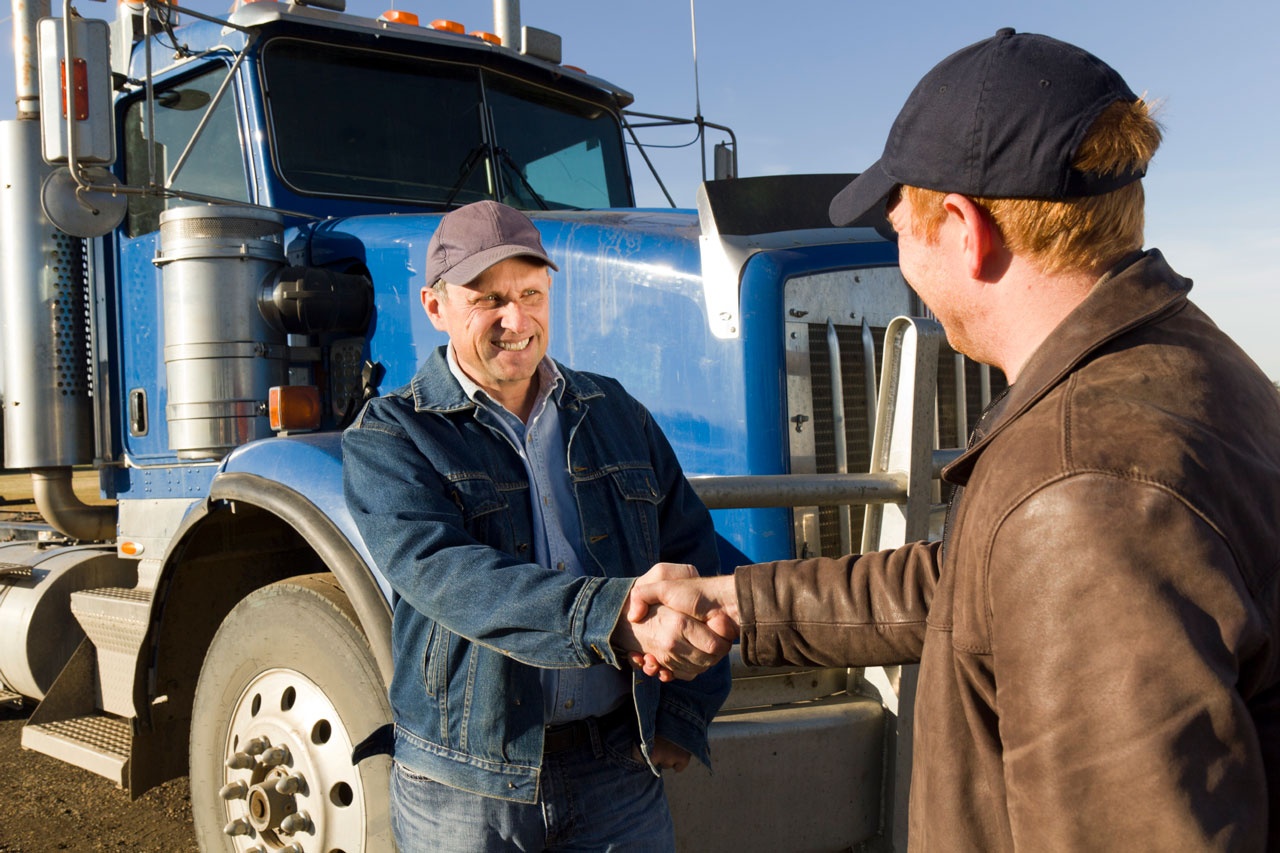
Behind every fleet that has a proven record in safety, lie sound and effective policies that are rich with carefully planned strategies and processes. But the details of a robust safety policy aren’t developed overnight. Much of what makes an effective safety policy so great is the amount of consideration and planning that goes into crafting the details (which can sometimes be years in the making) as a solid policy.
Automotive Fleet reached out to three of its 2016 Fleet Visionary honorees to better understand what makes their fleet policies tick. Honorees are individuals who have brought a new perspective to running a commercial fleet, resulting in a fleet that is safer, more operationally efficient, cost effective, or any combination of these.
Keeping Drivers Trained
One concept that is unanimously stressed in a fleet safety policy is thorough and consistent training. But training, how it relates to a fleet safety policy, is a broad concept. Safety training can represent a number of different processes, which includes, but is certainly not limited to:
- In-vehicle training
- Online training modules/videos
- Face-to-face discussions with managers
Dave Rush, senior manager EHS & fleet, Reynolds American Inc. (RAI) Trade Marketing Services, which is a new division of tobacco company R.J. Reynolds, said that one of the focuses of his fleet safety policy is where he’ll conduct in person training with drivers. These face-to-face workshops have fleet drivers across the U.S. sent to the RAI home office for training. Rush will also give manager workshop coaching, where those who are newly promoted to a field manager position are educated on the best practices of how to manage drivers, including an emphasis on how to promote and educate driver safety.
Rush, who works alongside Karen Delach, fleet and safety manager, RAI Trade Marketing Services, in the fleet management department will also occasionally perform site visits at locations across the U.S. where he’ll visit company drivers to give one-on-one coaching.
Another key element to Rush’s policy is computer based training. The company offers its own in-house training modules, which are training sessions
structured to curb the most common accidents that the fleet has experienced.
Indeed, Abe Stephenson, fleet and administration manager at DISH also offers training modules that are developed in-house.
“We typically don’t need to buy or use external training content because we’ve got a team here that does such a good job. It’s a full team of professionals that creates the content internally,” said Stephenson.
DISH also offers video -based training services.
Scott Lauer, associate director, North American Fleet Administration, Merck, also offers a very stringent training policy, which also focuses on online training modules. His team will also send out a monthly safety newsletter.
The newsletters, for Lauer, are a key component to the fleet’s policy, since the content is suggested by the drivers themselves.
“It’s not just the fleet manager doling out what the topic is each month. These ideas come from the drivers themselves and the drivers’ managers,” he said. “It provides some motivation that folks really have an input into it.”
Consistency Is King
But considering that there are many parts that make up a fleet safety policy, its key for an organization to ensure they are regularly communicating the standards within the company.
“When you roll out a program and people see that it’s not going to go away, I think it really is truly effective for the culture of the company,” said Lauer of Merck.
In addition to sending out the aforementioned monthly newsletters, Lauer of Merck said that the online training sessions Merck offers are assigned to drivers on a quarterly basis.
Similarly to Merck, Rush said RAI Trade Marketing Services also rolls out its computer based training quarterly, which helps propagate the organization’s safety policy to the team throughout the year.
Further still, Stephenson of DISH said that safety messaging is enforced all through the year via training exercises. These sessions include seasonality training and weather-related training, which are deployed via the company’s video training. The training modules and videos are assigned to DISH fleet drivers across the U.S. to ensure all of its drivers are receiving the same type of training.
“Once you’re consistent, I think the word gets out, and people start to take things more seriously, like distracted driving, cellphone use, seatbelt use, and a host of many other things,” said Stephenson.
In addition to consistency, there must also be an evolutionary aspect to the policy. What was once considered a safe practice today might be banned for fleet drivers in the future.
“Overtime, you may realize there are some gaps in the policy, or certain interpretations aren’t as clear, so I think the safety policy has to be a living document that is reviewed periodically,” said Lauer. “We’re about to take a hard look at some policies that maybe we want to make more strict and stringent, and maybe there are policies that maybe don’t work as well.”
This is a process that Lauer has instilled in his fleet. For example, cellphone use while driving used to not be considered an egregious offense for Merck. Now, however, any cellphone violations are considered egregious and automatically put the driver in the highest risk category, where remediation includes telematics for one year, additional training and a written warning.
Being consistent, however, not only means that the fleet needs to regularly keep an eye on specific driver related behaviors on a day-to-day basis, it also means that the fleets should pull driver motor vehicle records (MVRs), at least annually.
“We do annually, but we also have a self-reporting requirement, where drivers are required to self-report any moving violation or any infractions,” said Lauer. “Once a violation is reported we let about two weeks go by and we’ll pull an MVR for that driver to verify their infraction that they self-reported. And then when we do our annual MVRs if it turns out someone did not report an incident, then that’s a big deal, and we make a big deal of it.”
For Rush, his fleet will also do MVR reviews annually, but will review high-risk driver MVRs twice a year.
Bringing New Drivers Up to Speed…
Proper training early on in the hiring/employment process is crucial, as this will help establish the foundation for which all drivers are expected to uphold. Indeed, hiring capable drivers is essential, according to Rush of RAI Trade Marketing Services.
“You really got to be selective when you’re hiring the right candidates,” he said. “If you don’t have a very well structured pre-employment screening process, you’re doomed from the start.”
He said training employees that already have bad driving habits prior to hiring can be a difficult process, which makes driver screening crucial.
But once you’ve recruited the right players for your team, properly initiating the drivers to the safety program is critical.
“For new hire employees we do have a road course test for them which our different training centers and local offices will execute with a new hire,” said Stephenson of DISH. “So they get hands on training from internal folks, and all through the year, safety messaging is reinforced.”
Rush also includes new driver training as part of his one-on-one training sessions. He also said that all new hires receive telematics on their vehicles for coaching purposes.
…And Slowing Down the High-Risk Drivers
For the instances in which a driver becomes a “high risk” for a fleet, rigorous education and proper disciplinary action must be established.
For Lauer of Merck, high-risk drivers are removed from their assigned territories followed by a fact-finding of their offenses, which the driver must establish before he or she is permitted to drive for the company again.
Regardless of the infraction, if drivers get into the high-risk category, Lauer’s fleet will implement things such as telematics into a vehicle for driver monitoring as well as a lot of behind the wheel training.
“The goal is not to punish a driver in any way. The goal is to give the driver additional skills that are going change their behavior and improve their skills to make them a better driver,” said Lauer.
Rush of RAI has a similar mentality when it comes to remediating high-risk driver behavior.
“When someone has gotten some tickets or has been involved in a few collisions, we’ve deemed them to be a ‘high risk.’ When they’ve progressed to this point, there is a corrective action that takes place, but its more for their benefit,” said Rush. “The discussion is focused on the idea of: ‘You’ve broken this barrier now and we need to step in.’ And as I always tell them, if you’re not considering your own safety, it’s time that we step in and help you change some of your habits.”
Rush said this is when his fleet will implement telematics into the driver’s vehicle, as well as have their field managers conduct a monthly discussion on drivers safety with them. Rush, may also do off-site, one-on-one training sessions with high-risk drivers.
The Role of Technology
Following the idea of telematics, the fleets also place a heavy focus on the technology that is implemented into their driver’s vehicles.
Stephenson of DISH said that he focuses a great deal of keeping his fleet safe in a proactive way via Mobileye’s radar technology.
“It’s an ‘eye’ that’s attached to the windshield, and it can detect roadway lines, it can see the movement of vehicle. It knows distances and speed between vehicles and the vehicles in front of the driver,” he said. “With it, there is a core set of alerts we employ, which includes forward collision warning and lane departures warnings.”
While some of these features are standard on some new model vehicles for certain OEMs, Stephenson said his fleet employs several other safety features that aren’t typically standard on all newer model vehicles, including a tailgating alert, and a speeding indicator.
He compares the new in-vehicle safety technology that has been established in the last few years to being as essential as seatbelts and airbags.
“We want to try to rely a lot on letting technology help us whenever we can,” he said.
Further still, Rush of RAI said that his company will not put employees in a vehicle that does not employ some of the latest safety technologies. He said that it’s mandatory that drivers have the safety features activated on their vehicles whenever they are out in the field.
“We tell our drivers in our policy those safety features must remain on when the vehicle is in motion,” Rush said. “We will not allow them to go in an override safety features.”
Of these safety features, Rush says that the blind spot indicator technology has been the most well-received of the in-vehicle technology available in his fleet.
Stephenson also added that technology is going to play a large role in how the future of safety in fleet plays out.
“I think more and more, you’re going to see technology play a role in what we’re doing and what we need to be doing,” he said. “The policies and programs are important, but I compare it to seatbelts and airbags that you want to employ technology to help people who make mistakes.”
Rush added that the consideration of in-vehicle technology will be an important component to how fleet policies are developed in the future.
“I see the future is adapting your program to the technology that your car has,” he said.
Measuring the Effectiveness of the Policy
But with all these policies, processes, and technologies in place, there is much that must be taken into consideration when trying to measure a fleet’s success in safety.
For Stephenson of DISH, because his fleet’s safety policy has a heavy emphasis on proactive technology, a lot of how its success is measured depends on the data they obtain from the technology.
“Using Mobileye, we set a forecast that we were going to reduce our accident costs by x percent, whether that was a combination of avoiding accidents in their entirety or reducing the severity if we do get into an accident,” he said. “We have a whole set of multi-year, baseline data that we have for trending and just compare that with the trend of actual vehicles that have Mobileye.”
Rush of RAI said that measuring success in fleet safety can be difficult, because his fleet strives to be as proactive as possible. He said being proactive is mostly aided by telematics systems they utilize.
“We really try to do it on a proactive basis. We’re constantly running reports on a monthly basis. We’re looking at driver profiles, the severity of accidents, and looking at insurance claims. We’re constantly massaging the data to determine which direction we need to take and unfortunately that is a reactive approach, but it’s just very difficult, we don’t have a crystal ball.”
Getting Complete Company Buy-In
But with everything taken into consideration, ensuring that a fleet has total corporate buy-in is what will ultimately allow the fleet to establish its safety goals in the first place.
“Sponsorship is terribly important with anything like this, and you really need to get executive buy-in for several processes,” said Stephenson of DISH. “For companies, it’s probably a requirement in terms of if you’re going to be spending money on something; several groups usually require approval to do that.”
These processes helped Stephenson’s fleet have such a strong emphasis on utilizing the Mobileye technology, he said.
Rush said that having buy-in is probably the most important on the senior leadership level and the human resources department.
“The senior leadership has to lead by example; they’ve got to demonstrate that safety is important. And your human resources group has to have the policies to enforce it,” he said.
However, he said that the area that has the most responsibility in term of fleet safety is the division managers.
“They’re the ones that have the expectations from senior leadership to meet all of the sales goals. You’ve got to make it happen and then you’ve also have to keep your employees trained, there’s a lot of responsibility on their shoulders,” he said.
Indeed, Lauer of Merck said the senior managers who look over fleet drivers have their compensation partially dependent on the safety performance of the driver’s.
Bringing it to the Foundation
But what it really comes down to is how much effort the fleet manager puts into establishing the policies.
“Usually the fleet managers have a unique role, and there’s not a ton of people that have the same visibility of fleet safety,” said Stephenson of DISH. “So it’s the responsibility for us as fleet managers to figure out these things, and what works well. Proofing it out, doing the sales pitches, and due diligence.”
However, beyond being diligent and forward-thinking, the fleet manager should be empathetic with their drivers. Ultimately, these policies are designed to support the well-being of the driver.
“We truly care about them,” said Rush of RAI. “One of the things I do in my workshop is I’ll show them some of the assets they use to do their job, and I’ll ask them: what do you think the most valuable asset to this company is? I tell them it is our employees. So we really stress that from the top leadership all the way down. We stress to them that ‘you are the most valuable thing that we have.'”